Plastic injection molding uses a plunger to force hot, molten plastic material into a mold cavity. This solidifies over time into a shape that conforms to the contour of the mold. To use the part, the plastic material needs to solidify and cool down; this part of the manufacturing process takes time.
In a typical mold, cooling is achieved by passing a fluid through channels inside the mold so that the heat is conducted out of the plastic part, through the metal tool and into the fluid in the cooling channel. Conventional cooling channels are machined in straight lines using machining operations like drilling or milling, which severely limits the reliable cooling equally across the mold.
This is where conformal cooling comes into play. It is an innovative technology that elevates the cooling channels to a different level and is transforming the die and mold-making industry.
Here’s what I’ll cover in this article:
What is conformal cooling?
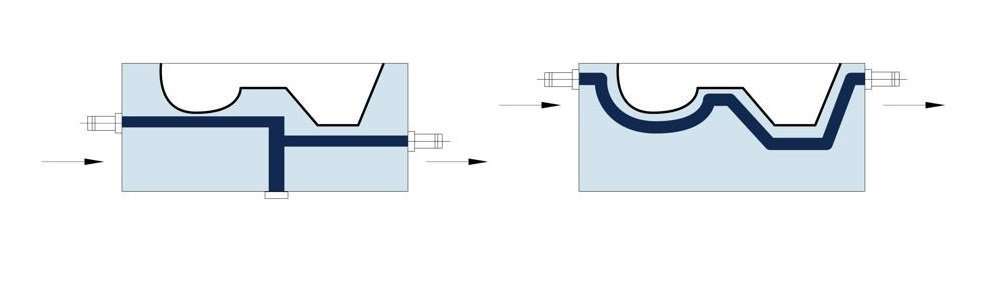
What are the benefits of conformal cooling?
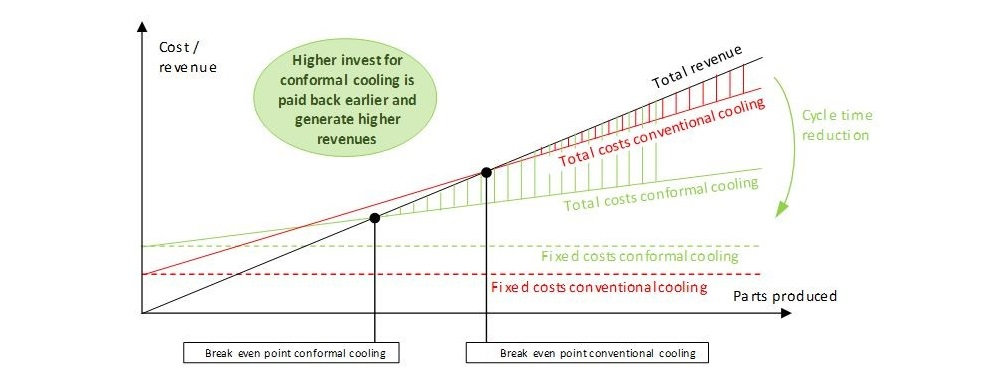
How can you achieve conformal cooling?
Conformal cooling makes use of additive manufacturing in a way that cooling channels can be curved and closely follow the geometry of the plastic part in the mold or core. It helps to reach hot spots and promotes temperature uniformity in the plastic materials being molded and reduces cycle times, uneven cooling, warpage and scrap.
Traditional or conventional tooling, due to its manufacturing methodology, is not able to achieve the shapes, paths and channel geometries that are made possible with conformal cooling. Looking at the images below, conventional molds have straight-line cooling channels (left), whereas conformal cooling (right) makes use of cooling lines in an injection mold that curve and closely follow the geometry of the part.